Magnetic Fluid
Magnetic fluid or ferrofluid is a colloidal liquid filled with nanoscale magnetic particles of magnetite (of only 5-10 nm in size). These magnetic particles cause the attraction (adhesion) of magnetic fluid to the magnet. Magnetic particles are covered with a protective film. It prevents the magnetic particles from clumping or sticking with each other.
Ferrous fluids have both the reaction (response) to the applied external magnetic field and fluidity. These unique features allowed ferrofluid application as “live” hermitizing systems (ferrofluidic seals) for vacuum, semiconductor, biological and chemical applications (see pic. 1).
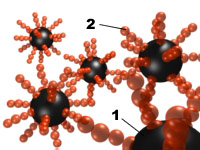
1- magnetic particle
2- protective film
Ferrofluid Seal
Magnetic fluid or ferrofluid seal is developed for sealing rotary shafts of vacuum processing equipment and agitating equipment (biological and chemical reactors, fermenters). Most often ferrofluid seals provide better operating and life span characteristics in comparison to other types of seals. This can be proved by the example of vacuum and special chemical media. Ferrofluidic seal is able to endure pressure drop up to several atmospheres both in dynamic and static mode and also to endure vibrational and shock load. At the same time magnetic fluid remains stable and is suspended in the seal by a permanent magnetic field.
The simplest traditional design consists of stationary casing connected to the reactor’s body, frictionless bearings, annular permanent magnet, pole pieces, sealed shaft and magnetic fluid suspended in the annular gap between pole pieces and shaft (see Pic. 2).
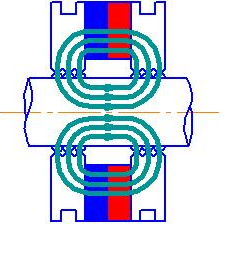
Principle of Operation (see Pic. 3)
Magnetic circuit created by stationary pole pieces and rotating shaft produces a magnetic flow in a gap between pole pieces and a shaft. The teeth on the surface of the pole pieces facing the shaft concentrate non uniform magnetic field thus suspending magnetic fluid in a gap. Magnetic fluid in a gap forms a hermetic liquid O-ring. Applied pressure can’t move or splash the magnetic fluid out of the gap.
The force opposing the pressure depends on the magnetic properties of magnetic fluid and value of magnetic field in the working gap.
Vacuum rotary motion feedthroughs are one of the most typical magnetic seals applications. These feedthroughs have several teeth at the pole pieces. Usually one tooth can withstand pressure differential up to 0.25 atmospheres while the whole rotary motion feedthrough can withstand pressure that is equal to the sum of pressure differentials endured by each tooth. Helium leak rate is about 10-12m3Pa/s. There is virtually no friction between rotating and stationary parts due to the sealing medium being a fluid so the seal does not wear. More than that, the magnetic seal produces no wear products leading to the systems contamination as there is no mechanical friction between static parts of the seal and the shaft.